An essential element to every rotationally molded part is the mold. Every rotational molder utilizes molds for this type of manufacturing and having a mold shop on site is a great asset to a rotomolding facility.
Mold making and rotational molding design go hand in hand. The skillful execution of both of these elements produce the most efficient manufacturing. Once the part to be rotomolded has been designed the process of creating the tool or mold can begin.
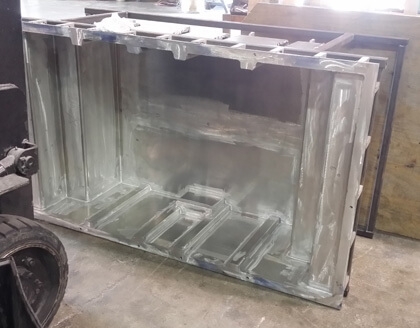
Most molds for rotomolding are cast or fabricated from steel or aluminum. Molds can have multiple chambers creating double wall parts or designed for multiple part manufacturing. How well a mold functions contributes to the quality of the parts manufactured and making changes to a mold or occasional mold repairs are a common part of rotational molding.
Mold making is a specialized process that sometimes requires design adjustments to be made. The mold shop at Granger Plastics Company fabricates, repairs and makes adjustments to tooling on site, working closely with the engineers who designed it. Timely changes can be made without the worry of shipping a mold. Having a mold shop in house also allows for preventative maintenance to be suggested, further reducing manufacturing costs.
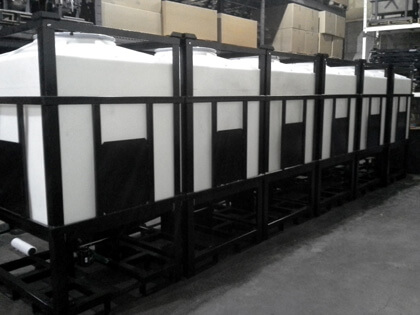
The mold shop at Granger also supplies additional metalwork for many products, allowing assembly costs to be kept to a minimum. Granger Plastics Company offers full service mold design, fabrication and maintenance to its customers all within our manufacturing facility, for the most cost efficient tooling and manufacturing possible.
Developing a custom rotationally molded product requires skill and attention at each step and finding a rotational molder able to complete the process from beginning to end can save time and money. For your custom rotational molding needs contact Granger Plastics Company at 513-424-1955 or visit www.grangerplastics.com to find solutions beyond expectations.